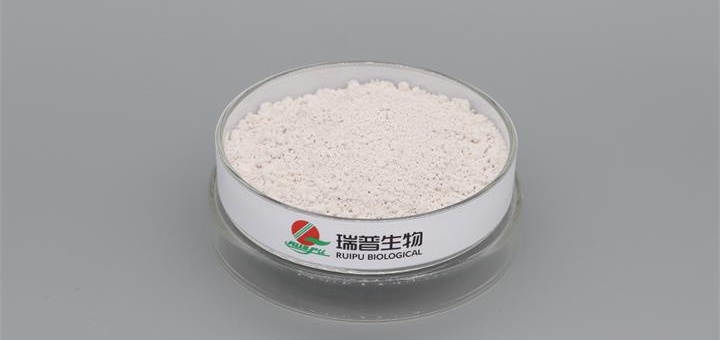
The drying and crushing-classification processes of ferric phosphate are critical steps in its production. Below is a detailed introduction:
I. Drying Process
Ferric phosphate requires drying during storage and handling to maintain its stability and performance. Specifically:
·High temperatures accelerate its oxidation, leading to loss of activity.
·Humid environments may cause ferric phosphate to absorb moisture and agglomerate, affecting its use in subsequent processes.
Common drying methods include:
1. Oven Drying: Heating ferric phosphate in an oven to evaporate moisture. This method is simple to operate but may require longer drying times and higher temperatures.
2. Fluidized Bed Drying: Using fluidized bed technology to suspend and agitate ferric phosphate particles in hot air, achieving rapid and uniform drying. This method is highly efficient but comes with higher equipment costs.
3. Vacuum Drying: Heating ferric phosphate under reduced pressure to evaporate moisture at lower temperatures. This method allows drying at lower temperatures but involves higher equipment costs.
4. Hot Air Drying: Using heated air to remove surface moisture from ferric phosphate. This method involves simple and cost-effective equipment but may require higher temperatures and longer drying times.
Key considerations for drying:
·Temperature Control: Ensure the drying temperature does not exceed the decomposition temperature of ferric phosphate to avoid performance degradation.
·Humidity Control: Maintain low humidity in the drying environment to prevent moisture absorption and agglomeration.
·Uniform Heating: Ensure even heating during the drying process to prevent localized overheating or underheating.
·Regular Maintenance: Conduct regular inspections and maintenance of drying equipment to ensure proper operation and effective drying.
II. Crushing and Classification
After drying, the solid ferric phosphate material needs to be crushed to achieve the desired particle size. The crushing-classification process typically includes the following steps:
1. Coarse Crushing: Using jaw crushers or hammer crushers to break block materials into smaller particles.
2. Fine Crushing: Using ball mills, vibrating mills, or jet mills to further grind the coarsely crushed material into the required size range.
3. Classification: Using classifiers to separate the finely crushed material into the desired particle size distribution. Classifiers can sort and separate particles based on size, shape, and density characteristics.
Key considerations for crushing and classification:
·Selecting Suitable Crushing Equipment: Choose equipment based on production requirements and material characteristics to ensure efficiency and product quality.
·Controlling Particle Size: Adjust equipment parameters and classifier screen sizes to control the particle size of ferric phosphate to meet the requirements of subsequent processes.
·Preventing Contamination: Avoid contamination from impurities and iron debris during crushing and classification to maintain product purity.
The drying and crushing-classification processes of ferric phosphate are critical steps in its production. By adopting effective drying and crushing-classification techniques, high-purity, uniform-particle ferric phosphate products can be obtained, meeting the application requirements in fields such as batteries and catalysts.