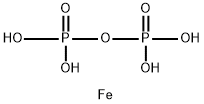
The impact of the price fluctuations of ferric pyrophosphate raw materials on downstream manufacturing enterprises is mainly reflected in the following aspects:
I. Production Costs:
Cost Increase: When the price of ferric pyrophosphate raw materials rises, the direct production costs of downstream manufacturing enterprises will increase. If enterprises are unable to promptly pass on the increased costs to the product prices, their profit margins will be squeezed. For example, in the food industry, enterprises that produce infant formula milk powder use it as an iron fortifier. If the price of ferric pyrophosphate rises and the price of milk powder cannot be increased accordingly due to market competition and other reasons, the enterprise's profits will decrease.
Cost Decrease: If the price of ferric pyrophosphate raw materials drops, the production costs of enterprises will decrease. With the product price remaining unchanged, the profit margin will expand. Enterprises can enhance the market competitiveness of their products by reducing costs, or invest the cost savings in other aspects such as research and development and marketing.
II. Production Planning:
Output Adjustment: Fluctuations in raw material prices may lead enterprises to adjust their production plans. When the price of ferric pyrophosphate rises, enterprises may reduce production output to avoid excessive costs. If an enterprise expects the price increase to be short-term, it may choose to maintain a lower production output and wait for the price to fall back; if it believes that the price increase is a long-term trend, it may consider finding substitutes or adjusting the product formula. Conversely, when the raw material price drops, enterprises may increase production output to fully utilize the advantage of low costs and increase market share.
Inventory Management: Price fluctuations will also affect the inventory strategies of enterprises. When the price of ferric pyrophosphate rises, enterprises may reduce their inventory holdings to lower inventory costs and price risks; when the price drops, enterprises may appropriately increase their inventory to meet future production needs and also enjoy the benefits of low-price procurement. However, an increase in inventory will also bring problems such as rising warehousing costs and capital occupation, which require comprehensive consideration by enterprises.
III. Product Quality:
Quality Stability: Fluctuations in the price of ferric pyrophosphate raw materials may affect the choice of raw material suppliers by enterprises. If an enterprise chooses a raw material supplier with a lower price but unstable quality in order to reduce costs, it may have a negative impact on product quality. For example, in the pharmaceutical industry, it is used to produce some iron-supplementing drugs. If the quality of the raw materials is poor, it may affect the efficacy and safety of the drugs. Therefore, even in the face of fluctuations in raw material prices, enterprises need to ensure that the ferric pyrophosphate they purchase meets the quality standards to ensure the stability of product quality.
Quality Improvement: On the other hand, when the price of ferric pyrophosphate rises, enterprises may pay more attention to the quality and usage efficiency of raw materials. By optimizing the production process, improving the product qualification rate, and other means, they can reduce the raw material cost per unit of product, thereby making up for the cost pressure caused by the price increase to a certain extent and also helping to improve product quality.
IV. Market Competitiveness:
Price Advantage: If enterprises can maintain the relative stability or competitiveness of product prices through effective cost control and procurement strategies during the price fluctuations of ferric pyrophosphate raw materials, they can gain an advantage in market competition. For example, in the feed industry, enterprises that use ferric pyrophosphate as an additive, if they can avoid increasing product prices or increase prices less than their competitors when the raw material price rises, they can attract more customers and expand their market share.
Product Differentiation: Fluctuations in raw material prices may also prompt enterprises to increase their investment in research and development to develop differentiated products, so as to reduce their dependence on the price fluctuations of a single raw material. For example, enterprises can develop products that use other iron sources to replace ferric pyrophosphate, or develop products with higher added value, and improve their market competitiveness through product differentiation.