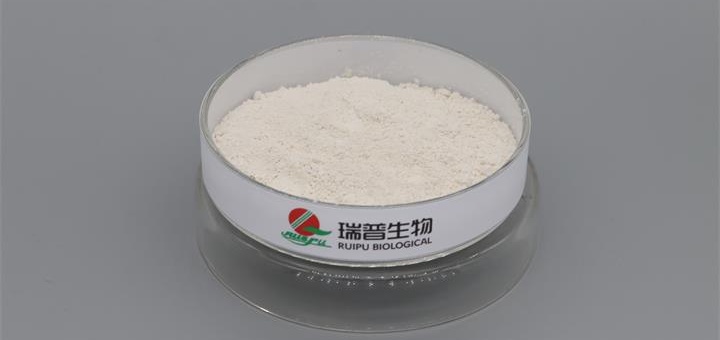
There are various production processes for ferric pyrophosphate. Different processes vary in raw material selection, reaction conditions, and equipment requirements, which directly affect the production cost. The following are the common production processes of ferric pyrophosphate and cost control methods:
I. Production Processes
1. Double Decomposition Method
Reaction Principle: A double decomposition reaction is carried out between soluble iron salts (such as ferric chloride, ferric sulfate, etc.) and sodium pyrophosphate solution to produce ferric pyrophosphate precipitation. The reaction equation is 2FeCl₃ + 3Na₄P₂O₇ = Fe₂(P₂O₇)₃↓ + 12NaCl.
Process Flow: First, dissolve the iron salt in water to prepare a solution of a certain concentration. At the same time, dissolve sodium pyrophosphate in water to make a solution. Under the condition of stirring, slowly add the iron salt solution to the sodium pyrophosphate solution, and control the reaction temperature and pH value to make the reaction proceed fully. After the reaction is completed, through processes such as filtration, washing, and drying, the ferric pyrophosphate product is obtained.
Advantages and Disadvantages: This method has a simple process, easy operation control, and high product purity. However, a large amount of by-products, such as chlorides or sulfates, are generated during the production process and need to be treated. Otherwise, it will cause environmental pollution.
2. Direct Method
Reaction Principle: Using iron oxide or iron hydroxide and pyrophosphoric acid as raw materials, ferric pyrophosphate is directly reacted to form ferric pyrophosphate under certain conditions. For example, 2Fe(OH)₃ + 3H₄P₂O₇ = Fe₂(P₂O₇)₃ + 6H₂O.
Process Flow: Mix iron oxide or iron hydroxide and pyrophosphoric acid according to a certain molar ratio, and add an appropriate amount of water or other solvents to make a slurry. Then, under the conditions of heating and stirring, the reaction proceeds. After the reaction is completed, the product is obtained through steps such as filtration, washing, and drying.
Advantages and Disadvantages: The advantages of the direct method are fewer reaction steps, relatively simple raw materials, and stable product quality. The disadvantage is that the reaction conditions are relatively harsh, requiring the control of a higher temperature and a suitable pH value, and the requirements for equipment are high.
II. Cost Control
1. Raw Material Cost Control
Optimized Procurement: Select suitable raw material suppliers and strive for more favorable prices through long-term cooperation, bulk purchasing, etc. At the same time, pay attention to the price fluctuations of raw materials in the market, and reasonably arrange the procurement plan to avoid cost increases due to rising raw material prices.
Raw Material Quality: Ensure that the quality of raw materials meets the production requirements, and avoid increased losses during the production process or a decline in product quality due to raw material quality problems. Although high-quality raw materials may have a higher price, in the long run, they can reduce production costs.
2. Process Optimization
Improve Reaction Efficiency: By optimizing reaction conditions such as temperature, pH value, and reaction time, improve the conversion rate and selectivity of the reaction, and reduce the waste of raw materials and the generation of by-products. For example, in the double decomposition method, precisely controlling the reaction temperature and pH value can make the precipitation of ferric pyrophosphate more complete and increase the product yield.
Energy Conservation and Consumption Reduction: Carry out energy-saving renovations on production equipment, and adopt efficient stirring equipment, heating equipment, etc. to reduce energy consumption. At the same time, reasonably arrange the production process, reduce the idle time of equipment, and improve the utilization rate of equipment.
3. By-product Utilization and Waste Treatment
By-product Recycling: For the by-products generated during the production process, such as sodium chloride in the double decomposition method, they can be recycled. Sodium chloride can be used in other industrial fields, such as the chlor-alkali industry, after purification, thereby increasing the added value of products and reducing production costs.
Waste Treatment: Reasonably treat waste water, waste residue, and other wastes during the production process to avoid fines and additional treatment costs due to environmental protection problems. Adopt environmentally friendly production processes and equipment to reduce the generation of waste, and classify and treat waste to achieve the maximum utilization of resources.