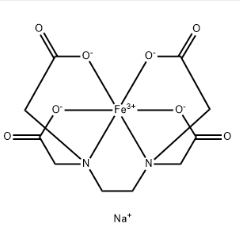
The extraction and purification process optimization of ferric sodium edetate (Ethylenediaminetetraacetic Acid Ferric Sodium) is a complex process involving multiple steps and parameters. Below is a detailed discussion of the optimization process:
I. Raw Material Preparation
1. Key Raw Materials:
·Traditional Process: Ethylenediamine, acetic acid, ferric sulfate, sodium hydroxide.
·Improved Process: Disodium EDTA (EDTA-2Na) and ferrous sulfate solution.
·New Process: Ferric oxide, iron powder, ferric sulfate, and sodium carbonate.
2. Raw Material Quality Control:
·Ensure raw materials meet relevant quality standards, with precise weighing and quality inspection.
·Control parameters such as molar ratios and concentrations to ensure reaction efficiency and product purity.
II. Optimization of Reaction Steps
1. Esterification Reaction (Traditional Process):
·Add ethylenediamine and acetic acid to the reactor in a specific molar ratio and heat to a certain temperature for esterification.
·Control the reaction rate and temperature to avoid side reactions.
2. Ester Hydrolysis Reaction:
·Mix the esterified acetic ester solution with ferric sulfate (or ferrous sulfate) in a specific molar ratio and heat to a certain temperature for ester hydrolysis.
·Control the reaction time and temperature to ensure complete hydrolysis.
3. Acid-Base Neutralization Reaction (Traditional Process):
·Add sodium hydroxide in a specific molar ratio to the acidic hydrolysis product in the reactor, then heat and stir for neutralization.
·Control the reaction temperature and pH value to ensure full neutralization.
4. Reaction Conditions Optimization (Improved Process):
·Determine optimal reaction conditions through experiments, such as reaction temperature, pH value, and reaction time.
·For instance, optimal conditions may include a temperature of 80°C, a pH of 7, and a reaction time of 1 hour.
III. Product Separation and Purification
1. Filtration:
·Filter the reaction solution to remove suspended solids and large impurities.
2. Crystallization:
·Concentrate the filtered solution and control temperature and stirring speed to precipitate ferric sodium edetate crystals.
·Separate the crystals through centrifugation or filtration.
3. Washing:
·Wash the crystallized product with an appropriate solvent to remove residual impurities.
4. Drying:
·Dry the washed product to remove moisture and obtain the final product.
5. Optimization of Purification Methods:
·Employ methods such as cold methanol recrystallization or other effective purification techniques to enhance product purity.
·Further optimize purification conditions, such as solvent selection, temperature control, and stirring speed, to achieve higher purity.
IV. Quality Control and Testing
1. Purity Testing:
·Use advanced instruments and rigorous analytical methods for comprehensive product testing and analysis.
·Common quality control indicators include product purity, moisture content, and heavy metal content.
2. Stability Testing:
·Conduct stability tests on purified ferric sodium edetate to ensure it remains stable under normal storage conditions.
V. Exploration of New Processes
1. Raw Material Substitution:
·Explore alternative raw materials or combinations to reduce production costs or improve product quality.
2. Reaction Pathway Optimization:
·Investigate new reaction pathways or catalysts to improve reaction efficiency and product purity.
3. Reuse of Mother Liquor:
·Recycle mother liquor to reduce resource waste and environmental pollution.
The optimization of the extraction and purification process of ferric sodium edetate involves raw material preparation, reaction step optimization, product separation and purification, quality control and testing, as well as the exploration of new processes. Through proper operation and stringent quality control, high-quality ferric sodium edetate products can be obtained to meet the needs of various fields.