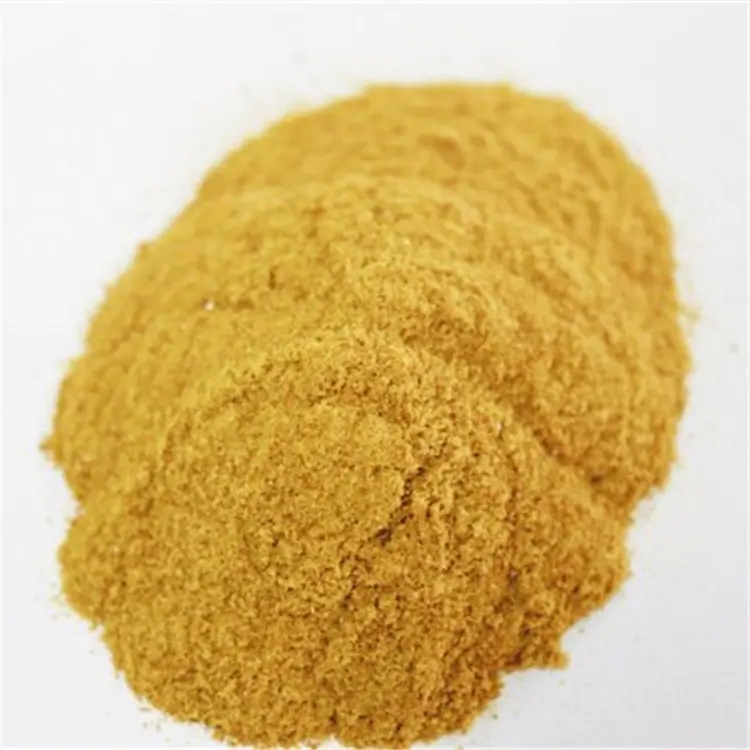
The preparation of ferric sodium edetate primarily involves the following methods:
1. Traditional Method
·Raw Materials: Ethylenediamine, acetic acid, ferric sulfate, sodium hydroxide, etc.
·Steps:
·Reaction of ethylenediamine with acetic acid: Esterification reaction to produce acetate esters.
·Reaction of ferric sulfate with acetate esters: Ester hydrolysis reaction to yield an acidified product.
·Reaction of sodium hydroxide with the acidified product: Neutralization reaction to form ferric sodium edetate.
·Post-Treatment: The product undergoes filtration, crystallization, washing, and drying to obtain ferric sodium edetate with high purity.
2. New Process Method
·Raw Materials: Iron oxide is used as the main raw material, with a reaction aid comprising a mixture of iron powder and ferric sulfate. EDTA and sodium carbonate are also added.
·Reaction Conditions:
·Optimal conditions involve adding the reaction aid at 5% of the iron oxide mass.
·The raw material molar ratio is n(EDTA):n(iron oxide):n(sodium carbonate) = 1:1:0.5.
·Reaction temperature: 90°C, Reaction time: 120 minutes.
·Advantages:
·Simpler process flow.
·High iron content in the product.
·Lower production cost.
·High product yield.
3. High-Purity Preparation Method
·Raw Materials: Tetrasodium ethylenediaminetetraacetate (EDTA-4Na), ferric chloride (or ferric oxide), sodium hydroxide, etc.
·Steps:
·In a reactor containing pure water, sequentially add sodium hydroxide, EDTA, and ferric oxide (or prepare ferric hydroxide first and then react with disodium EDTA).
·Maintain the reaction temperature at 80–100°C for complete reaction.
·Filter, concentrate until crystals appear, centrifuge to dehydrate, and dry the crystals to obtain the final product.
·Advantages:
·Simplified process, eliminating the need for chloride ion removal and decolorization.
·Shortened production cycle.
·Waste liquid output reduced by more than 50%, with mother liquor reusable in production.
·High product purity, suitable for large-scale industrial production.
4. Cost Analysis
The cost of ferric sodium edetate production involves the following factors:
·Raw Material Costs: The purchase price of raw materials, such as ethylenediamine, acetic acid, ferric sulfate, and sodium hydroxide, directly affects production costs. Variations in material purity and proportions also influence costs.
·Production Costs: These include energy consumption (e.g., water, electricity, steam), equipment depreciation, and labor expenses. Optimizing production processes, improving equipment utilization, and reducing energy consumption are key to lowering costs.
·R&D Costs: Developing new processes and technologies requires significant investment in funds and time. However, successful R&D can enhance product quality and reduce production costs substantially.
·Environmental Costs: Stricter environmental regulations require companies to allocate funds for wastewater treatment, gas emissions control, and other measures, contributing to higher production costs.
Various preparation processes exist for ferric sodium edetate. Enterprises can select the most suitable method based on their conditions and market demands. In cost analysis, companies should consider raw material costs, production expenses, R&D investments, and environmental compliance to devise efficient production plans and cost-control strategies.