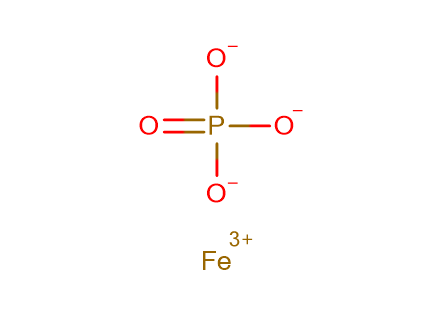
The preparation process of ferric phosphate mainly falls into two categories: wet process and dry process.
1. Wet Process
The wet process primarily involves the following steps:
·Preparation of Ferric phosphate Raw Material: High-purity ferric phosphate ore is selected as the raw material, crushed, and ground into a fine powder.
·Reactor Processing: Ferric phosphate powder is added to a reactor along with an appropriate amount of dilute phosphoric acid or acetic acid solution. The temperature and stirring speed of the reactor are controlled to ensure thorough reaction of the raw materials.
·Filtration and Separation: The reaction mixture is stirred, and a filtration device is used to separate the solid from the liquid.
·Drying Process: The filtered solid material is dried, typically using an oven or fluidized bed drying method.
·Crushing and Classification: The dried solid material is crushed to achieve the desired particle size.
Additionally, the wet process includes other synthesis methods, such as using mixtures of NH₃·H₂O and H₃PO₄ solutions with different concentrations. Strict control of the pH value of the mixture ensures the crystallization of FePO₄. The process begins with the formation of crystal nuclei, which subsequently grow into white precipitates.
2. Dry Process
The dry process mainly consists of the following steps:
·Preparation of Ferric Phosphate Raw Material: Similar to the wet process, high-purity ferric phosphate ore is selected, crushed, and ground into a fine powder.
·Mixing and Preparation: The ferric phosphate powder is mixed with a specific ratio of calcined phosphate lime, which reacts under high-temperature conditions to produce iron carbonate.
·High-Temperature Reaction: The iron carbonate undergoes a high-temperature reduction reaction. A certain amount of reducing agent is added in a reduction furnace, where the iron carbonate is reduced to iron powder.
·High-Temperature Precipitation: The reduced iron powder reacts with acid. Due to the electrochemical properties of the iron powder, the iron ions in the acid solution react with the iron powder, precipitating ferric phosphate.
·Subsequent Processing: The subsequent steps, including filtration, drying, and particle classification, are the same as in the wet process.
During the preparation process, it is essential to strictly control the reaction conditions and ensure the quality of the raw materials to obtain high-purity ferric phosphate with uniform particle size.
Application Prospects of Ferric Phosphate
Ferric phosphate, as an important chemical material, has broad application prospects across various fields:
·Lithium-Ion Battery Materials: With the rapid development of new energy vehicles and portable electronic devices, lithium iron phosphate batteries are highly favored due to their excellent safety, low cost, and long lifespan. As the cathode material for these batteries, the demand for ferric phosphate will continue to grow alongside the expansion of the lithium iron phosphate battery market.
·Catalysts: Ferric phosphate can serve as a catalyst in certain chemical reactions, promoting reaction efficiency. With the continuous development of the chemical industry, ferric phosphate's applications in the catalyst field will also expand.
·Ceramic Materials: Ferric phosphate possesses excellent thermal and chemical stability, making it a suitable additive in ceramic materials to enhance their properties.
·Nutritional Supplements: Ferric phosphate can be used as a nutritional supplement, added to bread, animal feed, and other products to provide essential iron for humans or animals.
Moreover, with the continuous improvement and refinement of ferric phosphate production technologies, market demand is expected to grow further. Particularly driven by the new energy vehicle and energy storage industries, the application prospects of ferric phosphate will become even more promising.