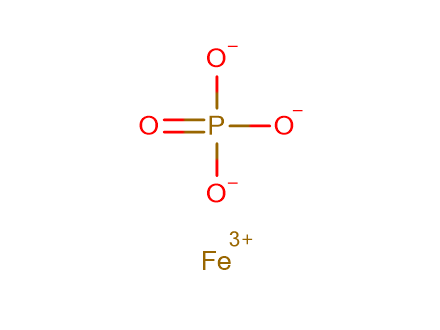
Ferric phosphate (FePO₄), also known as iron phosphate, occurs naturally in the form of vivianite, often containing two molecules of crystallization water. It is a white, pink, or pale yellow powder. Ferric phosphate has wide applications in metallurgy, electronics, chemicals, and other fields. Below is the production process and optimization strategies for ferric phosphate:
I. Production Process
The production process of ferric phosphate mainly consists of two methods: wet method and dry method.
1. Wet Method
The wet method process generally involves the following steps:
·Raw Material Preparation: High-purity phosphate rock or other iron and phosphorus-containing raw materials are selected, crushed, and ground into powder.
·Reactor Treatment: The raw powder is added to a reactor, along with a suitable amount of dilute phosphoric acid, acetic acid, or other acidic solutions. The temperature and stirring speed of the reactor are controlled to ensure complete reaction of the reactants.
·Filtration and Separation: The reaction mixture is stirred and then separated into solids and liquids through filtration.
·Drying Treatment·: The solid material obtained from filtration is dried, typically using an oven or fluidized bed dryer.
·Grinding and Classification: The dried solid is ground to the desired particle size.
·Packaging and Storage: The ground ferric phosphate is packaged in bags and stored in a dry, low-temperature environment to prevent moisture and oxygen from entering.
In addition, the wet method includes several specific methods such as the ammonium method, sodium method, iron powder method, fertilizer phosphoric acid method, red iron oxide method, and calcium hydrogen phosphate method. Among them, the ammonium method and sodium method are currently the most popular.
·Ammonium Method: Ammonia solution is used as the pH regulator, and the process involves the reaction of ferrous sulfate solution with monoammonium phosphate. Impurities are removed by precipitation and filtration, followed by neutralizing the excess acid produced in the reaction with ammonia solution to obtain pure ferric phosphate.
·Sodium Method: Sodium hydroxide is used as the pH regulator, and the process involves the acidification reaction of ferrous sulfate with phosphoric acid. Hydrogen peroxide is added to generate ferric dihydrogen phosphate. The pH of the reaction system is adjusted to about 2 with sodium hydroxide solution, resulting in the formation of pure ferric phosphate.
2. Dry Method
The dry method process generally includes the following steps:
·Raw Material Preparation: Similarly, high-purity phosphate rock or other iron and phosphorus-containing raw materials are selected, crushed, and ground into powder.
·Mixing and Preparation: The ferric phosphate powder is mixed with a certain proportion of calcined phosphate lime and reacted at high temperature to form iron carbonate.
·High-Temperature Reaction: The iron carbonate undergoes a high-temperature reduction reaction in a reduction furnace, where a certain amount of reducing agent is added to reduce the iron carbonate to iron powder.
·High-Temperature Precipitation: The iron powder is reacted with acid, and due to the electrochemical properties of the iron powder, the iron ions in the acidic solution react with the iron powder, precipitating ferric phosphate.
·Subsequent Treatment: The reaction mixture is filtered, dried, ground, and classified to obtain the desired ferric phosphate product.
II. Optimization Strategies
To improve the production efficiency and product quality of ferric phosphate, the following optimization strategies can be implemented:
·Optimization of Raw Material Proportions: Use the optimal raw material mix ratio to ensure complete reaction and maintain product quality.
·Optimization of Reaction Parameters: Improve thermal efficiency, shorten reaction time, and thus increase production efficiency. This includes controlling reaction temperature, stirring speed, and reaction time.
·Optimization of Crystallization and Removal Techniques: Reduce crystallization time and temperature to lower energy consumption, while improving crystallization efficiency and product quality by upgrading crystallization processes and equipment.
·Optimization of Thermal Strength: Use higher thermal strength to reduce grinding temperature, such as employing a melting process, which helps reduce energy consumption and improve production efficiency.
·Optimization of Control Parameters: Strictly control temperature, pressure, flow rate, and wettability parameters to prevent contamination of products and ensure product quality.
·Improvement of Production Equipment: Select appropriate reactor volume and number to ensure production progress and product stability. Avoid blindly pursuing large reactor volumes, which may affect product homogeneity and stability.
·Strengthening Environmental Protection Measures: Use environmentally friendly production processes and equipment to reduce the discharge of wastewater, waste gas, and solid waste. Additionally, strengthen wastewater treatment, waste gas purification, and solid waste recycling to minimize environmental pollution.
The production process of ferric phosphate is diverse, and the appropriate method and optimization strategy should be chosen according to the specific circumstances. Through continuous improvement of the production process and enhanced environmental protection measures, the production efficiency and product quality of ferric phosphate can be improved to meet market demand.