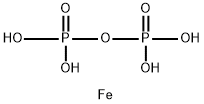
There are a variety of methods for the preparation of ferric pyrophosphate, and these methods can be optimized in a number of ways in actual production, as follows:
I. Preparation Methods
1. Direct Precipitation Method
·Principle: The iron salt solution and pyrophosphate solution are directly mixed under certain conditions, allowing iron ions and pyrophosphate ions to react and form ferric pyrophosphate precipitate.
·Procedure: Typically, iron salts such as ferric sulfate or ferric chloride are dissolved in water to prepare a solution of a certain concentration. Meanwhile, sodium pyrophosphate or other pyrophosphate salts are also dissolved in water to form a pyrophosphate solution. Under stirring conditions, the pyrophosphate solution is slowly added dropwise into the iron salt solution. The reaction temperature and pH value are controlled to ensure complete reaction, forming ferric pyrophosphate precipitate. The precipitate is then filtered, washed, and dried to obtain the final ferric pyrophosphate product.
2. Sol-Gel Method
·Principle: Using metal alkoxides or inorganic salts as precursors, a homogeneous solution is formed in an organic solvent or water. Through hydrolysis and polycondensation reactions, a sol is generated, which then undergoes aging and drying to form a gel. Finally, heat treatment converts the gel into ferric pyrophosphate.
·Procedure: Using iron alkoxide (e.g., iron isopropoxide) and an organic ester of pyrophosphate (e.g., tetraethyl pyrophosphate) as raw materials, they are dissolved in an appropriate organic solvent (such as ethanol) to form a uniform solution. A certain amount of water and catalyst is added to initiate hydrolysis and polycondensation reactions, forming a sol. The sol is aged at a certain temperature to promote further polycondensation and gel formation. The gel is then dried to remove solvents and moisture and subsequently heat-treated at high temperatures to convert it into crystalline ferric pyrophosphate.
3. Hydrothermal Synthesis Method
·Principle: Under high-temperature and high-pressure hydrothermal conditions, iron salts and pyrophosphates undergo a chemical reaction in aqueous solution to form ferric pyrophosphate crystals.
·Procedure: Iron salts and pyrophosphates are dissolved in water in a certain proportion to form a reaction solution. The solution is transferred into a high-pressure reaction vessel, sealed, and placed in an oven to react at a controlled temperature and pressure for a specific period. After the reaction is complete, the vessel is allowed to cool naturally to room temperature. The reaction product is then filtered, washed, and dried to obtain ferric pyrophosphate.
II. Optimization of Preparation Methods
1. Optimization of Reaction Conditions
·Temperature:
·In the direct precipitation method, increasing the reaction temperature appropriately can accelerate the reaction rate and enhance precipitation completeness. However, excessively high temperatures may lead to increased agglomeration of the product.
·In the hydrothermal synthesis method, temperature is a key factor affecting crystal growth and product properties. By optimizing the temperature, the crystal structure and particle size of the product can be controlled.
·pH Value:
·In the direct precipitation method, pH significantly affects the purity and particle size of the product. Controlling the pH within an appropriate range ensures a more complete reaction between iron ions and pyrophosphate ions, reducing impurity formation.
·In the sol-gel method, pH also influences the rate and extent of hydrolysis and polycondensation reactions, which in turn affect gel formation and product properties.
2. Selection and Optimization of Raw Materials
·Iron Sources:
·Different iron salts have varying effects on the preparation of ferric pyrophosphate. For example, ferric sulfate is relatively inexpensive but may introduce sulfate impurities, while ferric chloride has better solubility and higher reactivity but may leave residual chloride ions. Comparative experiments can help determine the most suitable iron source.
·Additives:
·Adding appropriate additives, such as surfactants or complexing agents, can improve product performance. Surfactants reduce surface energy, preventing particle agglomeration and resulting in more uniform particle size. Complexing agents can form stable complexes with iron ions, controlling their release rate and influencing reaction progression and product structure.
3. Process Optimization
·Stirring Speed and Time:
·In the direct precipitation method, stirring speed and duration significantly impact product particle size and morphology. Proper stirring ensures thorough mixing of reactants and uniform reaction but excessive stirring may break particles. Optimizing stirring time allows the reaction to proceed more completely, improving product purity.
·Aging Time:
·In the sol-gel and hydrothermal synthesis methods, aging time plays a crucial role in gel formation and crystal growth. Extending aging time facilitates further aggregation and growth of particles in the sol, forming a more uniform gel network, which benefits subsequent crystallization and enhances product performance.