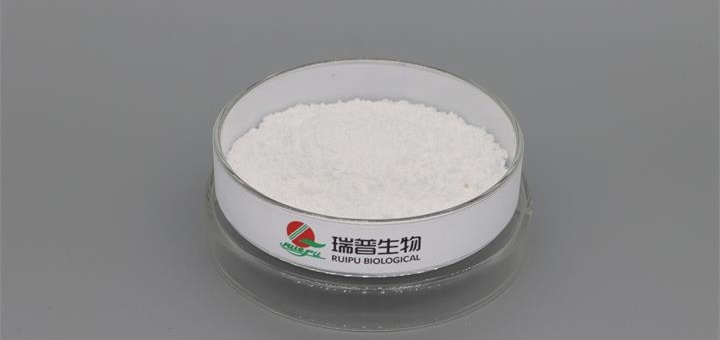
From Raw Materials to Finished Products: A Detailed Explanation of the Preparation Process of Zinc Gluconate
Zinc gluconate is a commonly used zinc supplement. The following is a detailed introduction to the preparation process of zinc gluconate from raw materials to finished products:
I. Raw Material Preparation
Calcium Gluconate: As the source of the gluconate radical, it is required to have high purity and low impurity content to ensure the product quality.
Zinc Sulfate: It provides zinc ions. Generally, analytical reagent grade or pharmaceutical grade zinc sulfate is selected to ensure that its indicators such as heavy metal content comply with relevant standards.
Concentrated Sulfuric Acid: It is used to adjust the acidity of the reaction system and catalyze the reaction. Industrial grade or chemically pure concentrated sulfuric acid should be used, and safety precautions should be taken when using it.
Activated Carbon: It is used for adsorption and decolorization to improve the purity and appearance quality of the product. Medicinal grade activated carbon is usually selected.
II. Preparation Process
1. Preparation of Gluconic Acid
Dissolve calcium gluconate in an appropriate amount of water to prepare a solution with a certain concentration.
Under stirring conditions, slowly add concentrated sulfuric acid and control the reaction temperature within a certain range (such as 50 - 60°C) for the acidolysis reaction.
After the reaction is completed, filter to remove the generated calcium sulfate precipitate, and obtain the gluconic acid solution.
2. Synthesis of Zinc Gluconate
Heat the obtained gluconic acid solution to a certain temperature (such as 70 - 80°C), add the zinc sulfate solution under stirring conditions, and continue to stir and react for a certain period of time.
During the reaction process, an appropriate amount of zinc oxide or zinc hydroxide can be added to adjust the pH value of the reaction system, so that the reaction proceeds in the direction favorable for the formation of zinc gluconate.
3. Purification
After the reaction is completed, add an appropriate amount of activated carbon to the solution for adsorption and decolorization to remove impurities and pigments in the solution.
Filter to remove the activated carbon to obtain a clear zinc gluconate solution.
Concentrate the solution to make it supersaturated, and then cool it for crystallization. Zinc gluconate crystals gradually precipitate out.
Centrifuge or filter to obtain zinc gluconate crystals, and wash them with a small amount of ethanol or water to remove surface impurities.
Finally, dry the crystals at a low temperature to obtain the finished product of zinc gluconate.
Ⅲ.Quality Control
Purity Detection: Use chemical analysis methods, such as complexometric titration, etc., to determine the content of zinc gluconate to ensure that its purity meets the requirements of relevant standards.
Heavy Metal Detection: Detect the content of heavy metals in the product, such as lead, cadmium, mercury, etc., through atomic absorption spectrometry or other appropriate methods, and require that their content is lower than the specified limit.
Appearance and Properties: Observe the appearance of the product, which should be a white or off-white crystalline powder, odorless, and slightly astringent in taste. At the same time, check whether its physical properties such as solubility meet the requirements.
During the entire preparation process, the reaction conditions, including temperature, pH value, reaction time, etc., should be strictly controlled to ensure the quality and yield of the product. At the same time, attention should be paid to the hygiene and safety of the production environment, and relevant operation procedures and quality standards should be complied with.